When it comes to 3D printing, Creality is one of the best players in the market. Their Ender product-lineup is so popular and cheap that you can’t resist to buy one. But how does it do? We bought an Ender 5 pro with the silent board from Creality and here is our verdict.
Buying process and delivery
We ordered the printer from the official Creality web site . The process was very straight forward. We selected the printer, we also added to card 2 Kg of PLA filament that was on offer and we proceeded with the checkout. The checkout process is using PayPal and as such we paid from our bank account via PayPal.
The order was shipped on the next day. It was split in 2 different deliveries. The first one was the 2 Kg filaments we had ordered and the 2nd one the actual printer itself. It turns out that Creality ships the printers and the filaments from different warehouses (at least in Europe).
Twelve days later the products had arrived in the front door of our offices. Although DHL services in our area are really bad and we have no preference in working with them, we didn’t had any complaint from Creality itself. They choose to ship the products with DHL and we can’t do anything about that.

Packaging
The Creality printer itself came in a very nice and careful packaging. The contents inside the box were placed in a kind of Styrofoam and were well packaged. After building the printer we observed a small dent in one of the aluminum profiles on the top frame. We were annoyed at start but it is likely that we may have done it ourselves during the build process. We really don’t know if the aluminums got delivered by Creality like this or it was our fault and and as such we can’t complain.

The packaging had everything inside and you will not need any screw drivers or other external tools. The printer came with a USB to SD card reader. An accessory that is very handy for us. Our desktop PCs don’t have an SD card reader and as such this small accessory solved a lot of headaches for us. Together with it was also an 8 GB SD card that included the software & firmware and which we used also to store our 3D prints.
Inside the box contents you will find a spatula which you will probably not need as the heated bed is magnetic and flexible allowing you to easily remove the prints. There are also a dozen of tire ups for cable management which are slightly small. We would prefer them to be an inch larger (2.5 cm) as they are small for the 4×2 cm aluminum profiles.
Along with the tools, there is also a plier in case you need to cut a tire up or the filament, 5 different sizes Allen keys (Hex keys) for tightening the printer screws, 2 wrenches, a screw driver, a 0.4 mm nozzle cleaner and a small bag with spare parts (nozzles, etc). Together with the tools, the printer came with a spool holder, a power cable and a small white PLA filament spool of 200 grams to do your first prints.

The printer has also an easily accessible voltage switch on the back side of the power supply of it allowing you to switch to either 230 V or 115 V. The front face of the power supply module has the power switch on the left, and on the right side an SD card reader and a micro-USB port to connect the printer directly to a computer if needed.

Assembly
The instructions in the manual are very simple. The manual has plenty of pictures and Creality has ensured to minimize the text. While assembling the printer we did a small mistake and we had to dismantle it and reassemble it again.
Creality’s manual indicates that the 4, 4×2 cm aluminum profiles need to be mounted vertically on the bottom frame of the printer. On the picture in the manual it has a small thumbnail picture in one of the 4 profiles that has a small hole in it. It wasn’t clear to us that this hole is a screw hole and needs to be on the top side of the printer for all 4 profiles.
After screwing the top frame with 4 screws in these 4 vertical aluminum profiles we realized that the rest 4 screws on the side could not fit because the profiles didn’t had any screw holes. When we realized that we had mounted the 4 profiles the other way around we unscrewed all 12 screws (8 on the bottom and 4 on the top) and we started the process correctly this time. Thankfully, the loss of time was not too much (probably 20 minutes). Creality also ensured to add a couple of extra screws for some parts in case you lose something.

The cabling of the device was also easy. There were letters on each cable (X, Y, Z and E for extruder) indicating where each cable should be connected. It took us around 5 minutes to realize how we should do the nozzle cabling connections but again Creality had ensured that they had correct colorings on their cables. As such making the process nearly impossible even for the most inexperienced person to connect wrong cables together.
The only complaint we might have in the cabling is that we wish that some of the cables would be some few inches larger. Some of the cables were barely in the correct size in order to route the cables and tie them up to the correct places. From our perspective, we are thinking to solder some extension cables to make them slightly larger and tidy up the cabling.

The rest of the building process gone flawlessly.
For an inexperienced user, s/he might find overwhelming the process of preheating, filament feeding and the bed leveling. Creality’s manual doesn’t give a lot of details other than the basics for these processes. For a first time user in 3D printing we expect that this process will take some time to understand it.
What we didn’t like during the build is that the Hot Bed was literarily hanging from 6 screws on the Z axis. As such, the front face of the bed during printing or bed leveling was slightly vibrating resulting in slightly distorted prints. It was something we knew it in advance before ordering the printer and we will have to live with it. Professional grade printers have 2 stepper motors lifting the bed from 2 different sides reducing vibrations and height differences between the front and back of the bed to the minimums. Of course, these printers are on a totally different price range compared to these low cost ones.

During the final building process we observed that the two belts that are moving the extrusion nozzle in the Y axis of the machine were loose. Creality hasn’t added any tensioning mechanism for the belts of the printer. There are four brackets on the four corners of the top frame on the machine. Unscrewing these brackets you can apply some pulling force manually with the hand and ensure that you have the correct tension to the belt. It is not an ideal solution of tensioning the belts but it works.
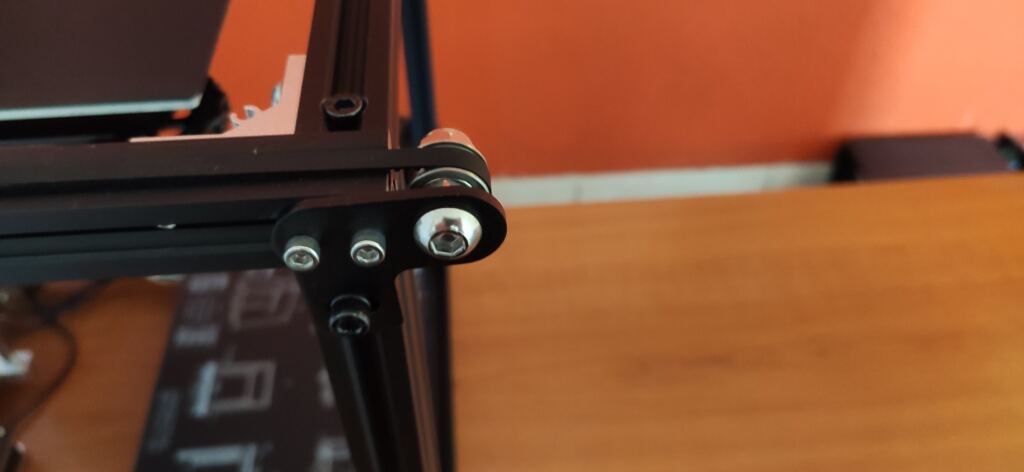
Software
Inside the SD card given together with the printer, there is a folder with all the appropriate software it might be needed. One of these software was the Creality Slicer 1.2.3. There are various slicer software on the market (Ultimaker Cura, the opensource Slic3r, Simplify3D, etc.). All these software require special configuration for each printer and we didn’t want to spend too much time for now.
We chose to install the default Creality Slicer software bundled on the SD card as Creality had already pre-included in the software the correct configuration for that printer. After installing and running the software, the Configuration Wizard popped up. We selected Ender 5 as a printer from the printers list and clicking the next button we finished with the wizard. The printer got configured automatically.

Next step was to open Thingiverse and download the classic 3D benchy STL file. Creality’s slicer software has an option for the dummies called Quick print. Having selected that option (it was on by default) we selected the material (PLA) and the Fast profile (0.2 mm). By mistake it seems that we also selected Raft on the platform adhesion instead of None. That was not an issue at all, it took benchy a little bit more time to finish printing.

After slicing the benchy, we clicked on the Save toolpath icon and we saved the .gcode file to the SD card. We then took the card, we inserted it to the 3D printer and we turned it on. We preheated the printing nozzle and the hot bed for PLA (200o and 60o Celsius respectively) and loaded the .gcode file to be printed. The print took around 1 hour and 20 minutes on the default speed settings.
The results
We were totally surprised with the results. The printer itself in the default settings prints (if not perfect) very well. The benchy had some minor stringing (middle image) on the top of its chimney probably due to the retraction of the printing nozzle at the end of the print.

On the print, you can clearly see the layer lines on the ceiling of benchy but this is because we selected the default Fast profile which has a layer height of 0.2mm. If we had selected the High quality or we had manually entered a layer height of 0.1mm or less we would have taken a benchy with almost no visible layer lines with the drawback of a greater printing time.
At a later time and while we were looking extensively this amazing printing result we got we observed some minor inconsistencies on the printing. These were not visible at all with a naked eye but only after very close inspection with a camera with good zoom factor.

We are not sure of why these inconsistencies were caused and we will definitely do some more extensive investigation later on to see if these can be fixed on later prints. PLA as a material is very easy to be printed. You could say that it is a kind of a hobbyist material since it does not require high bed and nozzle temperatures. Setting the printing nozzle temperature to around 200o Celsius and the bed temperature to 60o Celsius you can create some very nice prints.
On the other hand, printing with ABS requires much more elevated temperatures. ABS requires print nozzle temperatures of 210 to 250 °C and bed temperature between 80 to 110 °C. Apart from that difference, ABS has the tendency to warp a lot on the print bed giving more often inconsistent print results.
The bed size of the Ender 5 Pro is 220 x 220 mm and can accommodate print sizes up to 220 x 220 x 300mm. Although the bed size is not the largest we have seen in the market, it is enough to print most of the common objects compared to other printers that are having tiny bed sizes.
We want and we will definitely do some more extensive printing tests by using ABS or other materials to see the printing capabilities and the precision of the Ender 5. When we do the tests, we will ensure to update the article.
Operation
The printer has a manual bed leveling process. The bed has 4 turnable knobs on all 4 corners of the bed. As with all printers that have manual bed leveling, you move the print nozzle manually to each one of the four corners of the bed and you adjust the height of the bed in that corner by turning the appropriate knob. Having a piece of an A4 paper helps with the adjustment as you have to make sure that the nozzle lightly scratches the paper. This is because you want to leave a tiny space between the bed and the nozzle in order for the filament to get correctly extruded from the nozzle.
As stated above, due to the fact that the hot bed is hanging from a single Z axis it was difficult for us to correctly level the bed in the front of it with the 2 knobs. Even the slightest amount of pressure was enough to displace the front edge of the bed by a couple of millimeters making the leveling process almost impossible.
We know that the Ender 5 plus model from Creality has 2 different Z axis motor screws that are holding the bed in a firm position. Unfortunately, the plus model will cost you $200 extra than the Ender 5 pro model.
The printer itself comes with a magnetic flexible heated bed. After finishing the print, you can take the bed out of the printer and with a slight bend you can very easily remove the printed item from it. Then you can just install it back on the printer easily. It was a piece of cake!

We didn’t need any kind of a glue or other type of adhesive. The PLA from Creality that we printed did stick very well on the bed without having any adhesion problems. We also don’t know if over time the magnetic bed will start having any kind of adhesion problems due to usage but in the market you can always get supplied a new one. We also have a guess that these can also be cleaned with some kind of material (either water or isopropyl alcohol) but we will have to test it first to be sure that these doesn’t do any harm on the bed surface.
When we turned on the printer, we got surprised by the loud fan noise. We were expecting the 3D Printer to have a more quiet operation but this was not the case. The stepper motors themselves are not noisy at all – at least at the default speeds we were running them. We bought the printer with the silent board and as such the motors operation is almost inaudible. Although, we are sure that if we increase the speeds quite a lot we will also hear the steppers doing some noticeable sounds. But… the fans were so annoying that we were forced to move the printer far away of our work offices in a different room that no one could hear them.
Bellow are 2 YouTube videos in which you can observe the silent operation of the motors but not of the fans.
The verdict
We really enjoyed the purchase of the Creality’s Ender 5 pro 3D printer. The printer including a PLA filament of 2 KG set us back at around $416. It is not a large price if you consider the print quality that it gives.
The frame of the printer is very sturdy and of exceptional quality giving reliable prints on a very affordable price. The fan noise is something that we will investigate further. We don’t know yet if we can silence them by software and if that creates any kind of issues with the cooling and print quality. If we can not find a software solution we will definitely try to open them and clean them with some cleaning oil or replace them with some silent ones.
The bed leveling was slightly intricate but once you do it you don’t have to do it again. At least not so often. We also wanted a slightly better cable management but we can live with the current solution.
The bottom line is that we are excited by the printer and its abilities and we have no regrets of its purchase!
Comments
Loading…